Removing Retrofit Supply Chain Disconnect
NHMF Service Provider Forum membership represents the housing sector’s very best in innovation, best practice and collaboration. Embodying a broad cross section of organisations with differing interests and specialisms, from the large to the small providers, we are speaking to members and other stakeholders to find out more.
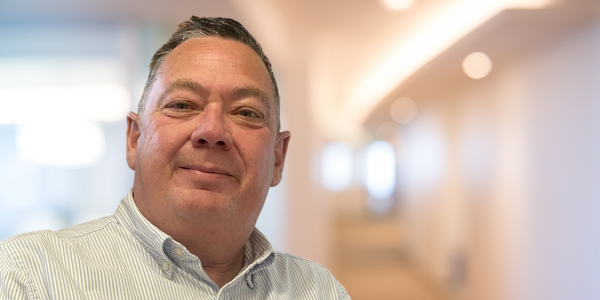
This month, we speak to Chris Pritchard, Projects Director at leading maintenance services company, CLC Group. Privately owned, CLC begin in 1969 and through a strategy of self-delivery with over 1000 employed operatives, the business has grown to its current £200 million turnover. Offering services to many sectors including housing, education, leisure, healthcare and commercial, 70% of CLC’s work comprises long-term partnering and repeat customers.
We began by asking Chris about his take-aways from the recent NHMF Study Tour in Oxford, a two-day event during which we visited Octopus Energy’s £10 million Energy Research and Development Centre in Slough, experienced Oxford’s Low Traffic Neighbourhood scheme, and had sessions at Oxford Brookes University on topics such as Damp and Mould, Indoor Air Quality and Building Overheating, Net Zero and low carbon construction research.
Chris comments on how what he saw during the Study Tour might play out in real life to help solve some of social housing’s current challenges. “A key focus throughout the Study Tour was on retrofitting our housing stock, decarbonisation, renewable energy and the innovations in progress to help in the fight against climate change. It was eye-opening to see how these innovations are playing out across the spectrum of different extremes in the supply chain spectrum, from commercial, local authority to academia.
Investing in product
At the commercial end of the spectrum, Octopus Energy’s decarbonisation plans are laser focused on the private housing sector. Octopus is investing big money into creating new products, which led to some really interesting debate on how collaboratively, we can make the solutions work and adapt them for our sector. This got me thinking about the underlying theme that come up throughout the Study Tour: the entire supply chain needs to work closer together for better results through opening lines of communication - which is exactly what the study tour allowed us to do.
Straight from the sharp end of the commercial market to the public sector when we visited Oxford Council’s Low Traffic Neighbourhood Scheme, introduced in order to lower vehicle emissions in the city. In this case, the opportunity for opening lines of communication was when we had the chance not just to be shown the scheme by the senior planning officer principally involved, but also to chat to residents about their views of the scheme.
A long way from lab to street
Next on the agenda, we delved into the world of academia at Oxford Brookes University. The clever research and development that’s happening in their labs is exciting, especially their focus on using different materials, like compressed cork and hemp, to create energy efficient building materials. There is so much potential here to help our sector, but whether it takes off or not is a different matter. It’s a long journey between the lab and our homes.
Joining the dots through collaboration
What really struck me is that the phrase The Retrofit Conundrum that’s used a lot in our sector, is so true. It is a conundrum of many moving parts that need to come together if we stand any chance of hitting Net Zero by 2050. Whether commercial or academic, community schemes or physical materials, all developing retrofit innovations for domestic decarbonisation works, need to be developed with an eye firmly on the end-user. For us, that’s the resident. Over the years, I have seen time and time again that nothing is better than speaking face to face with residents. We need to involve and get feedback from the people living their lives in the homes we’re improving. This is even more important when a lot of the retrofit works could be intrusive and disruptive, require education, explanation and hand-holding. It’s a far more complex sector than say kitchen and bathroom replacements. It’s also one that seems to come hand in hand with the need for levels of technological competency, e.g., apps to manage the heating, rather than just turning a dial up or down.
Break the cycle
Our first challenge is to get the right products for the right places that work for the right people in their homes, with everyone in the supply chain collaborating and buying-in. The collective supply chain from the energy giants to the universities to the contractors delivering the works, need to take a more cohesive and robust approach. Of course, once we have all these ducks lined up in a row, the next challenge is how to do actually deliver the right products to the right places? As a sector, we simply do not have enough skilled people. We’re already seeing ‘panic spending’ set due to the deadline imposed on the SHDF which will simply result in more sticking plasters, vanity projects and waste. But that’s a topic for a whole other blog.
For now, one of the most important things we can do is keep lines of communication open, share knowledge along the supply chain and not only do things right, but do the right things. CLC is a long-term member of the NHMF and were among their first conference exhibitors. We believe the forum is the best way to help keep these lines of communication open and remind us that the resident should always be at the heart of what we do. That way we can all sleep better at night.”