Lift maintenance and access equipment
This guide covers social landlords’ responsibilities for maintaining passenger lifts, access equipment and home adaptation equipment, such as hoists, stair lifts and vertical lifting platforms (‘through the floor’ lifts).
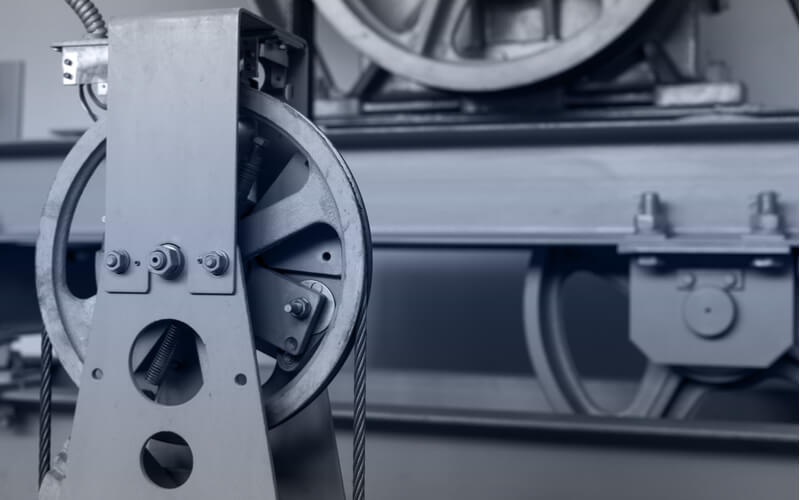
Lift maintenance and access equipment – Q&A briefing (updated November 2020)
Q. How does Lift maintenance and access equipment relate to the new Building Safety Bill?
Lift maintenance and access equipment is one of the factors that will need to be taken into account when developing the Building Safety case for each higher-risk building under the proposals in the Building Safety Bill. This will involve landlords assessing the safety of passenger lifts and other access equipment for each higher-risk building as well as ensuring compliance across all its stock for the safety of passenger lifts and other access equipment.
Q. What should social landlords do?
They should:
- appoint Building Safety Managers for each higher-risk building
- ensure that they have systems that will record the safety risks from passenger lifts and other access equipment and keep these risks updated for each higher-risk building as well as having systems to record compliance for the safety of passenger lifts and other access equipment across all their stock.
Q. Where can social landlords find more information on the Building Safety Bill?
The NHMF Best Practice website has detailed Q&A briefing on the Building Safety Bill.
Passenger lifts - Legislation and Statutory requirements
Landlords are responsible for maintaining passenger lifts and for carrying out periodic thorough examinations and inspections to ensure those lifts operate safely.
Section 3 of the Health and Safety at Work Act 1974 (HSWA) requires employers, such as landlords, to have responsibility for the health and safety of employees and people using or visiting their premises so far as reasonably practicable. While the Lifting Operations and Lifting Equipment Regulations 1998 (LOLER) do not apply directly to passenger lifts in residential premises, such a lift is primarily used by the occupants and not subject to the requirements of LOLER, However, businesses providing this equipment have responsibilities for its safety (i.e. it will require routine maintenance and inspection). To satisfy the requirements of the HSWA a similar regime of maintenance, inspection and examination to that required under LOLER may be considered 'reasonably practicable' in managing the risks (i.e. the risks may be the same as using lifts in connection with work. In addition, insurers may impose demands for similarly stringent levels of risk management to cover public liability.
The law requires that all lifts, when in use, should be thoroughly examined:
-
After substantial and significant changes have been made;
-
At least every twelve months or six months if the lift is used at any time to carry people, or in accordance with an examination scheme
-
Following "exceptional circumstances" such as damage to, or failure of, the lift, long periods out of use or a major change in operating conditions which is likely to affect the integrity of the equipment.
Note: When first installed, new lifts do not require initial thorough examination as long as they have been manufactured and installed in accordance with the Lifts Regulations and have a declaration of conformity, i.e. made not more than 12 months before.
A new lift is one where:
-
No lift previously existed;
-
An existing lift has been completely replaced; or
-
Only the existing guide rails and their fixings or the fixings alone have been retained.
Enforcement
In Great Britain the Health & Safety Executive (HSE) is responsible for relevant products under the Lifts Regulations 1997 for use in the workplace, and the Secretary of State is responsible for relevant products for private use. In Northern Ireland the HSE of Northern Ireland (hseni) is responsible for such products for use in the workplace and for private use. Health and safety legislation is enforced by HSE or hseni.
Housing Regulators
In England, the Regulator of Social Housing (RSH), requires registered providers to comply with its Regulatory Standards. On 1 October 2018 the RSH became a standalone public body, independent from the Homes and Communities Agency (HCA). On 11 January 2018, the HCA’s non-regulation arm adopted its new trading name Homes England. Managing lift maintenance and access equipment is covered by the Home Standard that requires meeting all statutory requirements for the health and safety of occupants.
In Wales all social landlords are required to meet and maintain the Welsh Housing Quality Standard (WHQS) as soon as possible, but in any event no later than 2020.
In Scotland, social landlords are required to meet the minimum Scottish Housing Quality Standard (SHQS) by 2015. Meeting the SQHS includes compliance with Technical Guide for healthy, safe and secure homes. The Scottish Housing Regulator expects compliance with all statutory and regulatory obligations including lift safety.
In Northern Ireland the Department for Social Development regulates registered housing associations under the Regulatory Framework for Registered Housing Associations in Northern Ireland 2006. Regulatory Standard 3.3 states that housing associations must develop, manage and maintain good-quality homes that seek to meet people’s needs and preferences now and in the future. This includes meeting the Decent Homes Standard and compliance with all statutory and regulatory obligations including lift safety.
Stair lifts - Legislation and Statutory requirements
LOLER (thorough examination) and PUWER (maintenance and inspection) apply only to stairlifts provided as work equipment for use by employees. Where stairlifts have been provided for residents, normally as part of an adaptation, landlords have responsibilities for the safety of all users under Section 3 of the Health & Safety at Work etc Act 1974. These may be adequately discharged by undertaking maintenance, inspection and a 6-monthly thorough examination.
All new stair lifts (either when first placed on the market, or first brought into use), are subject to the Machinery Directive / Supply of Machinery (Safety) Regulations. They must be constructed to be safe, supplied with Instructions, a Declaration of Conformity and CE marking. Those stair lifts which involve a hazard of falling from a vertical height of 3m or more are subject to Annex IV (item 17) of the Machinery Directive (so subject to conformity assessment as required by Article 12 (3) or 12 (4) of 2006/42/EC).
Compliance – good and efficient practice
HSE advises that routine maintenance typically involves checking and replacing worn or damaged parts, lubrication, and making routine adjustments. This is to ensure the equipment continues to operate as intended, and risks associated with wear or deterioration are avoided. Manufacturer’s guidance should be followed, especially where failure to do so might lead to harm.
If stair lifts are to be installed, residents should be assessed to see whether they are able to use them safely without assistance. Where a stair lift is installed in a Care Home and residents require help in using a stair lift, staff should be trained in its safe use and the best way to assist the resident. Stair lifts should comply with ISO 9386: and BS 81-40: Stair lifts and inclined lifting platforms for persons with impaired mobility.
Sometimes vertical lifting platforms are installed to help residents with impaired mobility bypass short flights of stairs. They should be manufactured to ISO 9386 Part 1: Vertical lifting platforms. Advice on the design, construction, installation, operation and maintenance of vertical lifting platforms is provided in BS 6440: Powered vertical lifting platforms having non-enclosed or partially enclosed liftways intended for use by persons with impaired mobility – Specification or BS EN 81-41 Vertical lifting patforms for use by persons with impaired mobility.
Other lifting and access equipment
LOLER applies to equipment that lifts or lowers loads as a principal function, and includes any accessories used in doing so (such as attachments to support, fix or anchor the equipment). This includes passenger lifts, hoists, bath lifts and slings, as well as a building cleaning cradle and its suspension equipment. However, fall arrest ropes are not covered by LOLER. Further details and examples of equipment covered by LOLER can be found in HSE’s Approved Code of Practice and guidance.
Compliance
HSE has published Thorough examination of lifting equipment - a simple guide for employers and Frequently asked Questions that explains the requirements of LOLER and what equipment the Regulations cover and, importantly, what equipment is not covered. It sets out schedules for thorough examination, when lifting equipment should be inspected and what is required for the non-lifting parts. It also explains what records should be kept. HSE’s Health and safety in care homes includes guidance on the use and maintenance of lifting equipment and stair lifts.
A competent person should determine the thorough examination scheme. They should have enough practical and theoretical knowledge and experience of the lifting equipment to enable them to detect defects or weaknesses, and assess how important they are in relation to the safety and continued use of the equipment. It is important to note that a thorough examination is not the same as regular servicing of equipment.
The interval between periodic thorough examinations should be no more than 6 months for lifting accessories and for equipment lifting people, and no more than 12 months for other lifting equipment, or as specified in a dedicated scheme of examination. The dedicated scheme of examination may often specify periods that are different (longer or shorter) from the ‘periodic’ thorough examination intervals (i.e. 6 or 12 months). It should also be thoroughly examined each time exceptional circumstances have occurred i.e. liable to jeopardise the safety of the lifting equipment.
If lifting equipment requires thorough examination, it must be carried out and recorded before lifting equipment is first used (unless there is written evidence that such an examination has already taken place). Where the safety of the equipment depends on the installation conditions (e.g. a tracked ceiling hoist), it must be thoroughly examined in situ before it is used, to ensure it is safe to operate.
Eyebolts
Eyebolts which are secured into a structure as an anchorage point for lifting equipment, e.g. a pulley block or abseiling ropes should normally be treated as an attachment for fixing or securing the equipment under LOLER. However, eyebolts fastened to a structure to secure fall arrest/restraint equipment are not lifting equipment and are not covered by LOLER. They should be considered as part of the fabric of the building and require inspection and certification every 12 months. (the Workplace Regulations may be relevant).